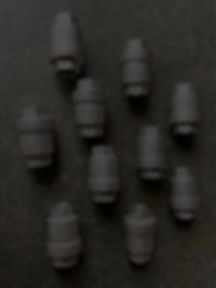
Specification

1. What is Spring Check Valve?
A spring check valve is a valve type that only allows the liquid to flow in one direction. It comes with two ports, inlet, and output. The Inlet port operates as a door opening and it allows media to enter the valve. Output port operates as an exit point and media flow from the valve body to external components through this port. It is called one-way valves or non-return valves. This valve's purpose is to prevent backflow in the system installation.
A spring check valve relies on a pressure differential to work which requires a minimum pressure from the inlet to operate the valve. The valve is closed when the output pressure is higher than the inlet. Unlike other valve types, it does not operate with a handle, lever, or electronic actuator, and no external control is required to work with the spring check valve. The spring check valve is commonly installed in a system that backflow would cause an issue. It is an effective, easy and cheap valve solution to solve a potential system issue. For example, a sewer line installs with a spring check valve to ensure that waste is not to re-enter the system. They are used if backflow will cause damage to equipment upstream which only allows media to flow in one direction. Spring check valves are ideal for numerous purposes in water system installation.
Spring check valve uses and characteristics:
-
Provide pressure relied on system and environment safety purposes.
-
Prevent contamination from reserve flow.
-
Protect equipment components from backflow damage.
-
No human intervention is required to function the valve.
-
Operate by flow and differential pressure with the assistance of valve spring.
2. The Spring Check Valve cracking pressure
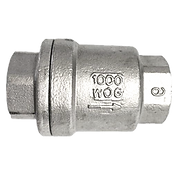
Cracking pressure refers to minimum upstream pressure to crack open the spring check valve. It is known as opening pressure. This minimum pressure is typically provided in pound per square inch gauge (PSIG) or BARS. The standard cracking pressure is 0.5 bar, 1 bar, or 2 bar. It is subjected to the overall valve operating pressure.
When the minimum pressure is larger than the spring compressive, it forces the valve to crack open bypassing fluid flow through. The higher the upstream pressure, the easier the spring pushes for valve opening. Cracking pressure is set by spring compression and this can be adjusted by manufacturer valve design to suit the application. The spring inside the check valve will “lift” when there is a minimum cracking pressure on the upstream side and this pressure is needed to overcome the spring tension. When the upstream pressure goes below the cracking pressure, the spring will close the valve to prevent back-flow in the valve body.
Spring Check Valve
3. When to use metal seat VS Viton seat Spring Check Valve?
The spring check valve comes with two sealing types, a Viton seat, and a metal seat. Viton or soft seats are generally made of fluoropolymer elastomer and synthetic rubber. They are good for an application where chemical compatibility is important and the sealing tightens quality is the key. Viton seals are not advisable for fluids systems that are abrasive or dirty as the Viton seat can break down easily and cause valve leakage.
The main advantage of a metal seated spring check valve over a soft seated spring check valve is the ability to withstand high temperatures. Metal seats can endure severe flashing, abrasive process fluid, hydraulic shock, and high temperatures up to 537 degrees. They are a good option for high corrosion applications too.
In general, the metal seated spring check valve has a variety of applications compared to the soft seat valve. Understanding the process conditions is the key to determine the right seat spring check valve.
4. What is the difference between Swing Check Valve and Spring Check Valve?
The swing and spring check valve have the same function which allows fluid flow in one direction. However, the valves have different components to control the flow. Spring check valve opening flow is controlled by spring and swing check valve is controlled by disc. The swing check valve is forced close by backflow and the spring check valve is closed by default where it required a minimum pressure to push down the spring.
Spring check valves are functional in vertical or horizontal installation. They provide significantly more versatility than swing check valves. It reduces the risk of a water hammer in which the spring is strong to ensure the required closure speed and it has a short-stroke length to ensure very fast and “slam-less” closure. The spring check valve device component keeps noise levels down during system application where the swing check valves could certainly exacerbate the issue.
There are some advantages of spring check valve:
-
Heat and cold resistance
-
Rapid flow interruption provides quick interruption of flow
-
Positive sealing even at a pressure below cracking pressure
-
Does not require gravity or backflow pressure to work
-
Spring accommodates a wide temperature range
-
Application in vertical or horizontal installation

BSPP SS316 Spring Check Valve
5. Which is the symbol of Spring Check Valve?
An arrow symbol on the outside of the spring check valve body indicates the flow direction. The spring check valve arrow is pointing in the direction of the pipe flow. To experience the optimization of the check valve, it is critical to adhere to installation best practices. A simple mistake in spring check valve installation can reduce system efficiency at best or cause substantial damage to the whole operation.
Some important points to take note of:
-
Selection – Select the correct valve according to your piping size, material, pipe orientation, flow direction, and flow rate will result in high efficiencies system performance.
-
Positioning – Pay close attention to where the valve is to install with the pipeline. It includes ensuring the valve is at least five pipe diameters away from fitting connectors such as elbow, tee, or another type of valve which can cause turbulence.
-
Orientation – Ensure the spring check valve is installed properly by checking the external arrow stamping which is printed permanently marked on the middle of the valve body. This arrow helps to identify the proper positioning relative to the piping line direction.
HOW TO INSTALL A SPRING CHECK VALVE

*** The spring check valve provides flexibility in installation location as it can be used in a vertical or horizontal way. Before installation, the main system is depressurized and purged to avoid danger in operation. Here are the important steps to install a spring check valve.
STEP 1
Determine the pipe outer diameter size and total length to create a reliable joining point.
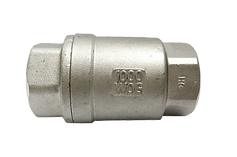
STEP 2
Check to ensure the pipeline is free of welding splashes.

STEP 3
Ensure the pipe is on the correct perpendicular axis so that the threads are tightened correctly with the other male thread. Hold the valve in the correct direction with a spanner or wrench while the piping threaded end is screwed in.

STEP 4
Assemble the pipes and spring check valve one at a time. Operate the pipeline from a small pressure and observe the threaded end connection.
